Nip Pinch Roller Pressure Measurement
Capture and measure nip pressure distribution with pressure mapping.
Nip Pinch Machine Setup, Roller Alignment, and Pressure Distribution
Tekscan tactile pressure sensors are excellent tools for measuring nip profiles, force or pressure variations along a roll axis. The software measures and displays in real-time the static forces in a pinch roll nip. For many large machines, nip contact is adjusted by setting hydraulic pressure at contact units located on the ends of the rollers. In the absence of measurements, the relationship between hydraulic pressure and nip force is assumed to be linear. Drag in the linkage and other sources of hysteresis are not quantified. Tekscan sensors measure nip force and width at locations along the axis at various hydraulic pressures providing real-time feedback on a PC. The detection of crowning and differences in pressures and contact width along the length of the roll can be documented. These measurements improve costs by reducing machine set-up time, down time and product scrap. Tekscan’s patented, thin-film, pressure sensors are available in different shapes and pressure ranges, are reusable, and provide accurate pressure data.Tekscan offers two solutions for nip and roller pressure measurement: I-Scan™ and NPAT™.
I-Scan Pressure Mapping System
I-Scan is a versatile solution for optimizing a process or manufacturing parameters. With a wide range of sensor form factors and data analysis tools in the software, I-Scan is a powerful tool for a research and development team to improve yield. More benefits include:- Ideal for engineering team analysis
- Used to understand full surface area of the nip
- Over 200 sensors to choose from in different shapes and pressure ranges
- Real-time display of pressure sensor data
- Recording & playback of dynamic pressure images
- Fast (100 Hz) sensor scanning
- Supports high temp sensors
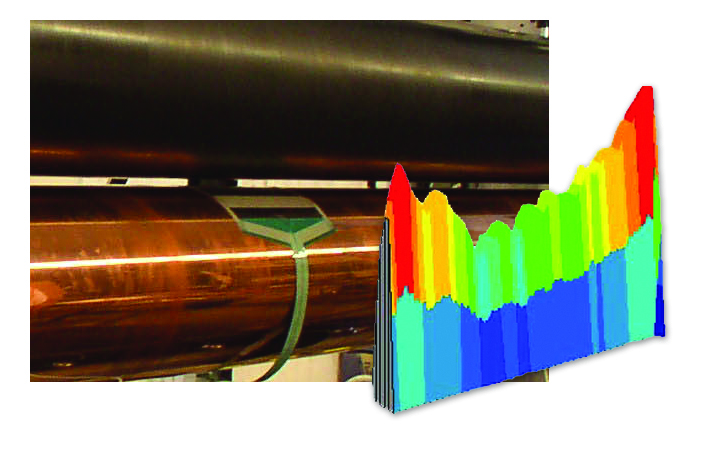
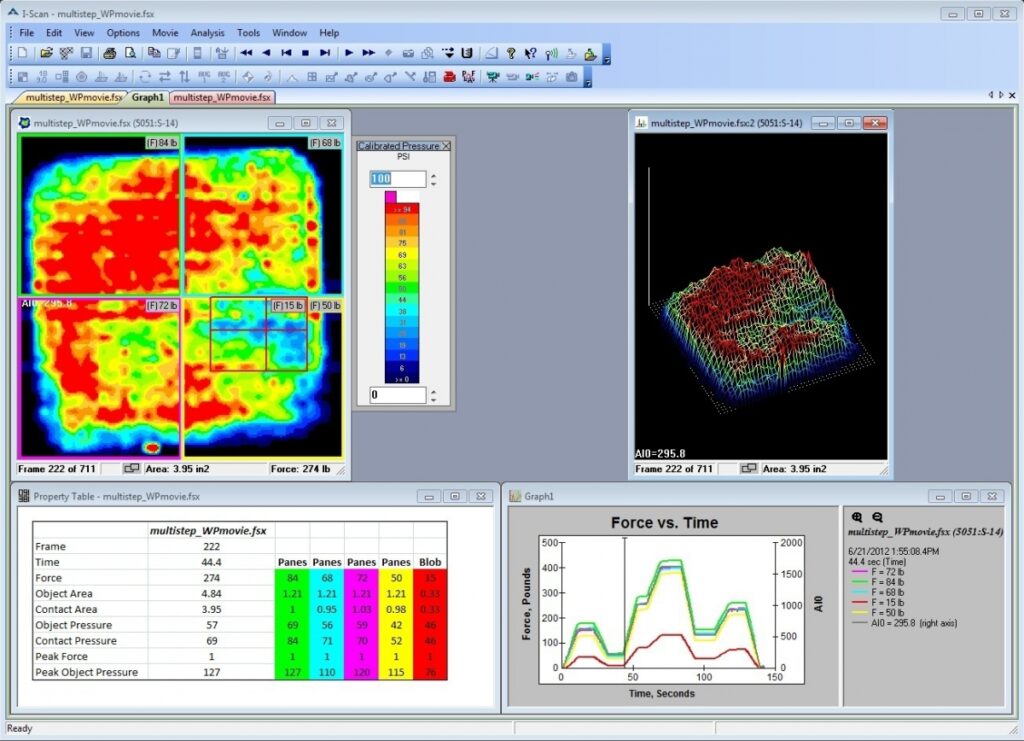
Nip Pressure Alignment Tool™ (NPAT™)
The Nip Pressure Alignment Tool™ (NPAT) is an easy-to-use tool used to capture nip footprints and relative pressure distribution between nip rollers. The system utilizes a sensor made up of an array of thin and flexible pressure sensitive bands, which can be configured to match the size of an application. More benefits include:- Clear visual representation of pressure distribution, nip width, and cross width using static snapshots
- Ensures proper nip alignment
- Ideal for large nip roller areas
- Prevents equipment and product damage
- Provides quantifiable and credible data
- Easily maintained in-field
- Allows for proper machine set-up, machine comparison, and preventative maintenance.
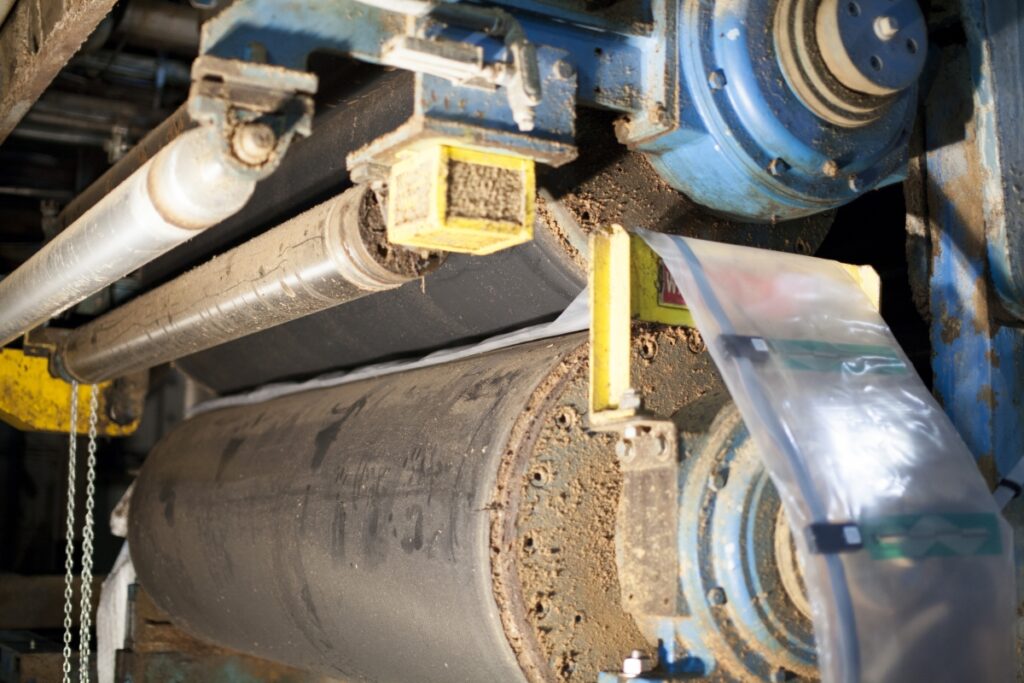
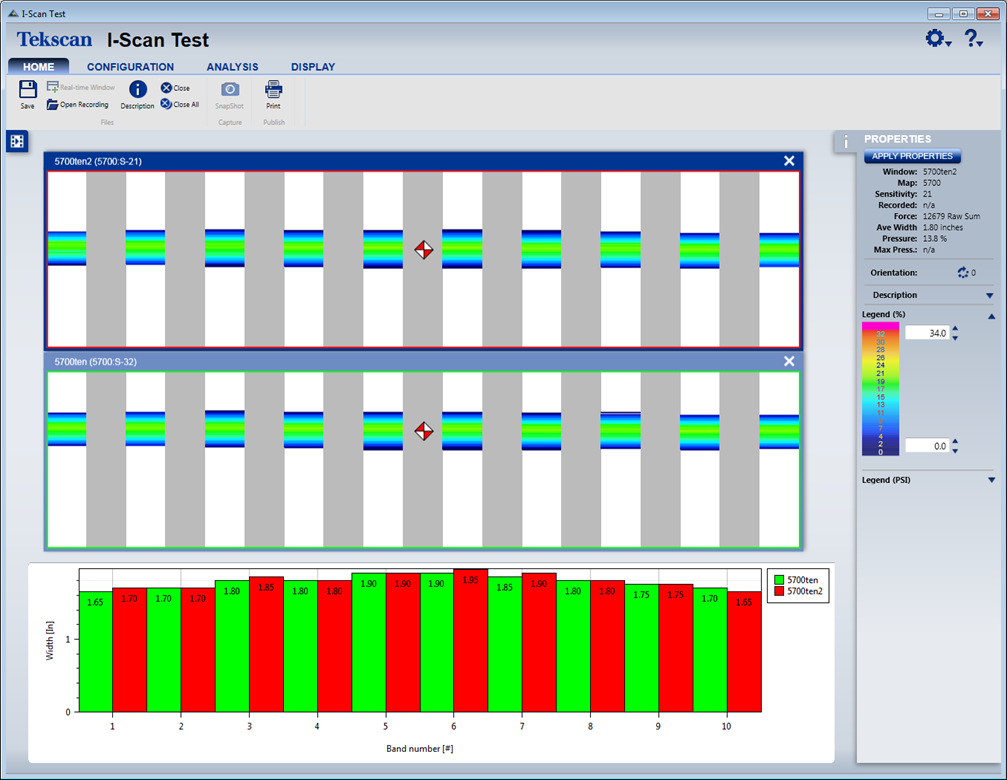
See how Pressure Mapping Technology can help streamline machine setup processes, like nip pressure alignment: